Blog · 5 MIN READ
Workflows at Work: Refractory Inspections During a Turnaround
Posted on November 16
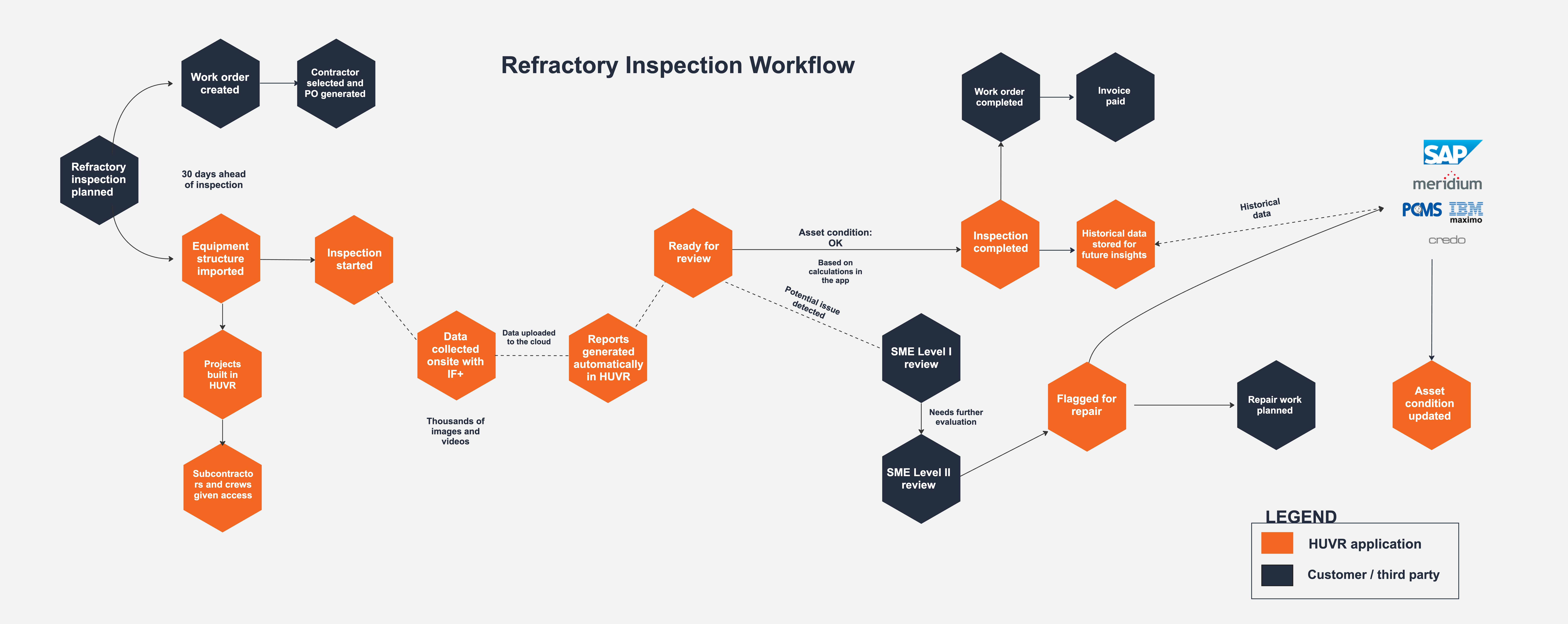
HUVR is proud to offer a wide range of inspection solutions that expedite and simplify your processes – each Workflows at Work piece in this series highlights one configuration of the near-infinite workflows that HUVR optimizes. Curious about the simplicity and savings as you read? Reach out to an expert to ask about replicating this success with your business today.
Refractory inspections are one of the most sensitive workflows that HUVR supports. Why, you ask? Because refractory inspections, typically completed during turnarounds, are time-sensitive operations that, if not done correctly, lead to extended downtime or future failures that result in costly unplanned shutdowns.
SET-UP
A refractory campaign on a new site can be implemented with as little as 15 days of lead time from equipment set-up to inspection creation and team training, thanks to HUVR’s world-class service. Once a refractory inspection is planned, HUVR will digitize your equipment structure and build a workpack project on each piece of equipment. All associated components to be inspected are built under the workpack as child projects.
In-house inspectors and third-party inspection service providers are assigned specific inspections and can securely log into the HUVR InspectFlow+ application on any iOS or Android device. Within IF+, they can view the parent and child projects in one place, and execute your standard inspection workflow. The same workflow can be used globally to ensure consistent data is collected at every site.
For each type of equipment and refractory, checklists are built out in a standardized format. By using set choices and language defined by the asset owner, inspections are performed consistently, and there is no guesswork trying to interpret results across different vendors.
Each checklist can be tailored to meet industry API standards and incorporates the individual company’s needs so that the organization can select from the level of inspection granularity needed (within industry guidelines, of course). This kind of workflow configuration means organizations essentially can manage their level of risk according to their cost and time needs while still remaining compliant with regulatory standards.
EXECUTION
As the inspector completes inspections on each component, they’re no longer limited to taking just one or two photos or using one person’s verbiage/descriptions of a sound or condition. Instead, with HUVR’s application InspectFlow+, inspectors can work offline and capture large sets of imagery and video. Calculations are also built into the application that provide direction based on the inspected condition to give your SMEs a comprehensive view of the refractory material.
Once in a location with connectivity, the findings are uploaded and stored in the cloud, avoiding double entry of data or hand copy errors. Once in the cloud, HUVR automatically generates a report with an elevated summary of the findings, and notifications can be sent to the appropriate executives or crew members to let them know the inspection is ready for the next stages of review and repair. Some SMEs might already be monitoring the progress from a HUVR customized dashboard where they can also see when inspections are completed promptly.
REMEDIATION
The automatically generated reports, complete with embedded full-resolution imagery and video, provide actionable insights for API 936-certified engineers to make quick, effective decisions regarding the assets in question. If the calculations in HUVR determine the asset to be in upstanding condition, the findings are reviewed and confirmed. If an issue is possibly detected, the findings are sent to the Level I SME for review where the asset is determined to either need a repair, leading to the development of a repair plan, or the asset is determined to need further review, in which case a Level II SME will review and make recommendations for repair and mitigation.
OUTCOME
The immediate upload of data and automatic reporting that HUVR provides exponentially decreases the review and execution time of your inspections. Combine this with savings realized during the planning stage, and HUVR can help organizations make decisions and complete turnarounds faster than ever before, and in a turnaround inspection where every day delayed means millions of dollars lost, every second counts. By conveying the unforeseen refractory surprises five times faster than in the traditional workflow, our clients can create a remediation plan, order materials, and perform repairs all without causing costly delays to the shutdown.
Want to see a demo of the workflow or speak with a successful client? Check out our on-demand webinar, Transforming Turnarounds: Discover HUVR and VEERUM’s 3D Contextualization Solution or schedule time with an expert here.