Blog · 8 MIN READ
Workflows at Work: Ultrasonic Testing for Piping Inspections
Posted on September 06
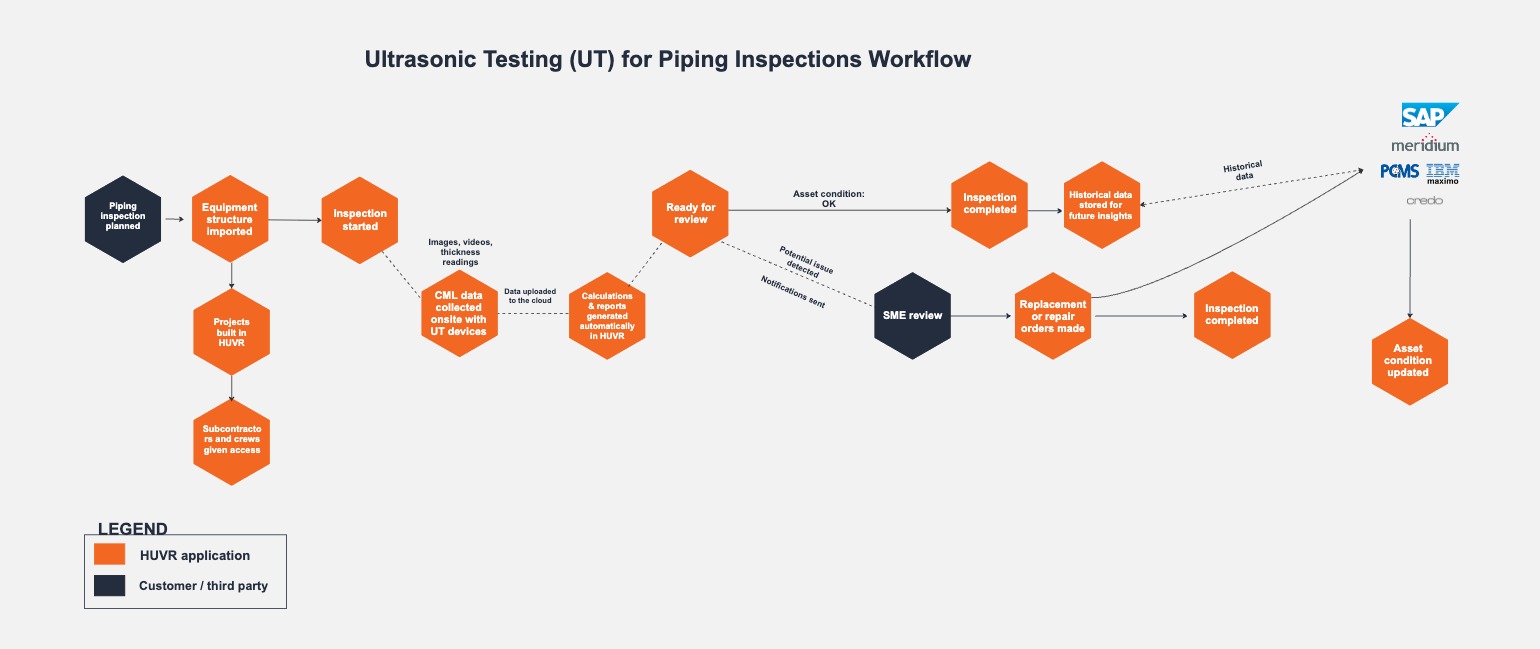
HUVR is proud to offer a wide range of inspection solutions that expedite and simplify your processes – each Workflows at Work piece in this series highlights one of the near-infinite workflows that HUVR optimizes. Curious about the simplicity and savings as you read? Reach out to an expert to ask about replicating this success with your business today.
Collecting data on condition monitored locations (CMLs) from a corrosion circuit can be a complex challenge in the field. Managing ultrasonic testing (UT) devices while completing measurements across a multitude of CMLs is often a balancing act for NDT Level II and III inspectors. Environmental factors interfering with UT device probes, unwieldy paper checklists for massive amounts of data, and common transcription errors can all contribute to a lengthy and complicated piping data collection process. Moreover, once these calculations and readings are taken and transcribed into a digital format, calculations and keeping a centralized historical record to inform future inspections and repair plans can be a less-than-efficient endeavor.
With HUVR’s all-in-one platform, say goodbye to data headaches. By seamlessly connecting to your UT devices, HUVR creates an end-to-end UT process that enables your inspection team to get started in seconds, capture field data with ease, make fewer errors along the way, and unlock long-term insights that drive smarter decision-making.
SET-UP
Project set-up is step one to digitizing your UT inspection workflows. Our world-class service team works together with you to craft equipment structures that optimize your site’s asset hierarchy. Any historical data can easily be imported, so that the last few readings can be accessed from the field. Commonly, projects are built for the common asset – the corrosion loop – and our team Scopes the CMLs to be inspected. In HUVR, Scope is the subset of CMLs that are selected for readings during an inspection. Scope sends just the CMLs you select down to the inspector for collection. Scope can be changed, expanded or reduced, to meet the dynamic inspection environment. The system then will automatically build sections for each component that has a scoped CML to keep the checklist organized and accommodate the variety of data points to be inspected at various times.
Checklists are configured to standardize the data collection process and accommodate the individual needs of each organization. This powers clean, standardized data in and clean, standardized data out for every inspection so that reporting is easy, consistent, and actionable. Each component has a clear section built out, with options for any material data needed: schedule, temperature, pressure, etc. as well as nominal data and installation dates. Any of this data can be made available to technicians within a project as needed to make informed decisions.
Sensitive customer data is safe in HUVR’s all-in-one Reliability Automation Platform. HUVR is SOC2-certified, and access to each project/data set is assigned on an as-needed basis so each member of the team has access to as much or as little information as they may need to be effective in their role. Views and dashboards are configured according to the needs of each individual group or technician so that asset owners can review progress and results in the office, technicians can access important CML data in the field, and SMEs can make actionable recommendations based on their findings.
EXECUTION
Once projects are set up and crews have been assigned, it’s time to conduct the inspection. Notifications that it’s time to inspect a piece of equipment can be sent on a regular interval in accordance with local regulations and the organization’s individual inspection scheduling standards.
Taking readings with a UT device and recording findings in the field can be a logistical nightmare for the average inspector, and calculations once back in the office can add time and errors into the mix for even the sharpest inspectors. With HUVR, teams are no longer slowed down by clunky logistics and manual calculations susceptible to human error. Technicians can now record findings directly into the InspectFlow+ app on any iOS or Android device, taking readings straight from the field and into HUVR.
Your team can take single or multiple measurements with their devices in the field, and the system records the measurement to your organization’s specifications, i.e the lowest, highest, or average of the readings. Photos or videos of CMLs can also be taken in HUVR to provide further context. Geolocation data is associated with each image/video so that you know which CML the data is located within, creating richer data sets and clarity for organizations looking to create long-term actionable insights.
When field users enter their readings for a CML, the app can automatically flag readings that may need further investigation. For example, if the reading today is larger than the past inspection, the inspector can be alerted to double check their measurement. This heavily reduces the chance of human error and frees up your technicians to focus on getting accurate readings and moving on to the next CML. Validation measures can also be set to different thresholds of loss that may require further investigation. This can save repeat trips as the technician can be alerted and make additional measurements while at the CML.
Progress throughout the planning and inspection process can be monitored via HUVR’s configurable dashboards and reports through the very end of the project to ensure accountability and clarity into technician progress and outcomes.
REMEDIATION
Calculations and reports are generated in HUVR once data collection is complete. Reports can be configured according to the needs of your teams, including embedded imagery and video, CML data, and calculations completed once back from the field. Short-term corrosion rates, long-term corrosion rates, and life remaining calculations are standard for UT inspections and automatically generated in HUVR once back from the field, but additional data can be reported as needed.
With HUVR’s seamless digital twin integrations using vendors like VEERUM and ZynQ360, your teams can also visualize the collected data in an integrated 3D model for more clear, quick, actionable insights. 3DHub optimizes performance visually: CMLs on a piping structure can be highlighted with colors to indicate the status of degradation for a section of the pipe. Historical data is overlaid on the modeled assets for a more visual picture of your asset health, and teams can make decisions more efficiently with a contextualized model of your CMLs.
Once the data has been reviewed by SMEs, the correct course of action to remediate the issue can be made. Remediation teams can be notified if degradation has reached a certain threshold or the life remaining calculations are low. Components can be repaired or replaced on the timetable of the organization’s choosing in order to stay compliant while optimizing repairs and replacements for the needs of your asset.
The historical data of CMLs is then saved in HUVR’s cloud-based platform indefinitely. Data can be shared with existing systems of record as well thanks to HUVR’s open API and set integrations with common systems. A historical chain of command now exists to inform your experts on when action may be needed again in the future, making it simpler and more efficient to make long-term decisions and plan around repeated patterns of wear and tear.
OUTCOME
By simplifying the inspection process, integrating with existing systems of record and cutting-edge digital twin providers, and providing rich standardized data to your teams, HUVR revolutionizes UT-based piping inspections. Teams using HUVR are safer, more efficient, and more reliable with their UT calculations than teams without. Automatic calculations heavily reduce chances of human error while validation measures and color-coded visualizations in 3DHub make it simple to make actionable decisions about a CML. Documentation all in one place paints a richer picture and helps teams stay compliant with the click of a button. Reduce inspection time, increase time on tools in the field, and make better decisions on your schedule with HUVR.
Want to learn more about our other cost-reducing workflows or speak with an expert to learn more? Check out our latest installment of the Workflows at Work series or schedule time with a HUVR expert here.