Blog · 7 MIN READ
Workflows at Work: Hazardous Area Equipment Inspections
Posted on February 29
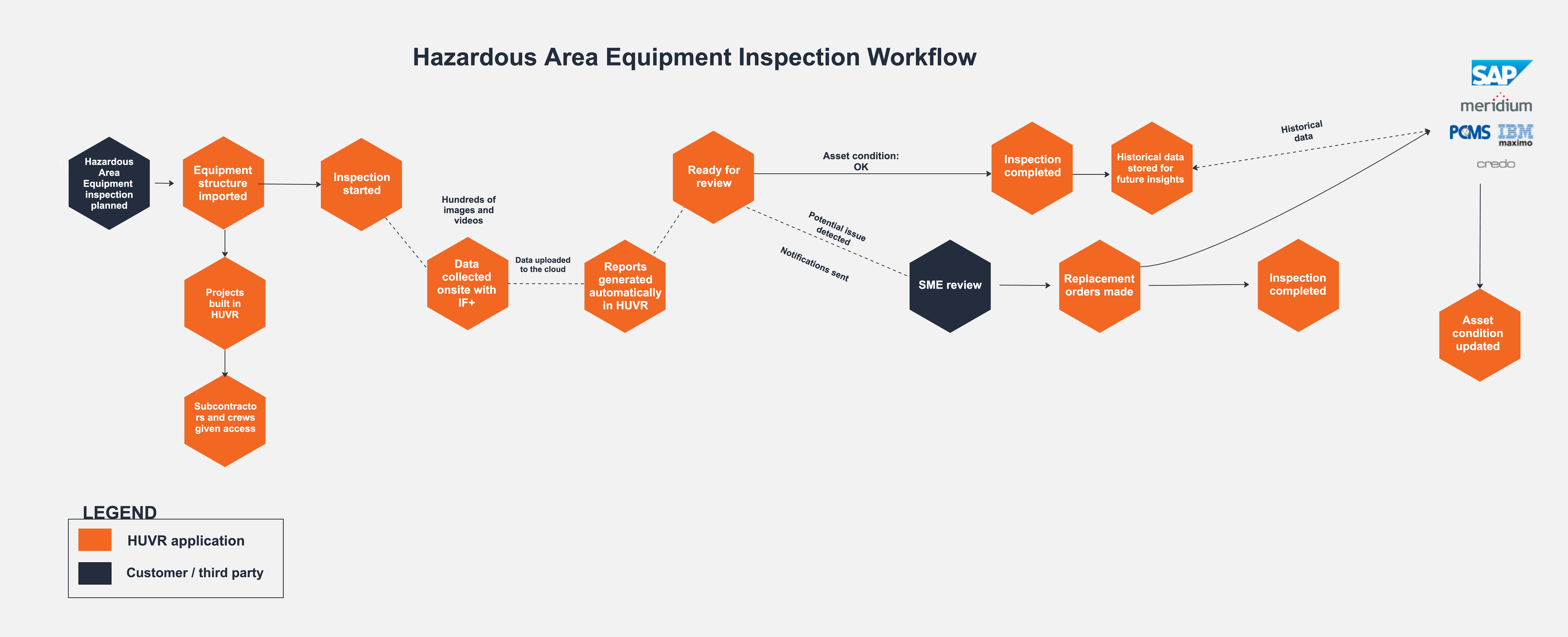
HUVR is proud to offer a wide range of inspection solutions that expedite and simplify your processes – each Workflows at Work piece in this series highlights one of the near-infinite workflows that HUVR optimizes. Curious about the simplicity and savings as you read? Reach out to an expert to ask about replicating this success with your business today.
Hazardous Area Equipment (HAEQ) inspections go by many names in the industry depending on where you sit globally; some organizations call them Electrical Equipment in Hazardous Area (EEHA) inspections, some call them EX inspections, and others stick with HAEQ. Whatever you call them, these inspections done on electrical equipment intended for use in explosive atmospheres are some of the most common – and arguably important – inspections conducted by asset owners and service providers that use HUVR.
To remain compliant with Occupational Safety and Health Standards (OSHA) standard 1910.307, organizations are required to conduct regular inspections of equipment in these dangerous, highly explosive areas. One wrong move – or spark – could be catastrophic for asset owners and service providers alike, potentially harming individuals on-site, destroying product and equipment essential to the operation of the company, and hemorrhaging money in replacements and fines.
These inspections, typically conducted every four years with random annual spot checks, have traditionally been done via paper checklists and are not often tracked in commonly used asset integrity platforms like SAP or Meridium. This makes inspections and reporting thereafter unwieldy, and historical data near-impossible to save and access. Asset owners and service providers using HUVR can overcome these hurdles by collecting specific field data with ease directly in the system, automated reporting, historical data, and actionable findings at the end.
SET-UP
From junction boxes to electrical outlets, control panels, and more, HAEQ inspections often involve large quantities of equipment with many different components. Subsequently, projects often need to be as granular as possible to ensure inspectors are collecting the right data from the right sources, something that other asset integrity systems often struggle with or simply don’t include in their program at all. Our world-class support team works together with asset owners to create workflows in HUVR tailored to the individual needs of the organization that follow regulatory guidelines so inspections are simple, standardized, and compliant.
Checklists for Class I or Class II HAEQ are built out in a standardized format that meets the local jurisdiction requirements. Pre-set choices and standard language defined by the asset owner result in consistent language and answers across all subcontractors. By using a combination of asset and project types in the HUVR system, asset owners can require and ensure that the correct, specific type of inspection is being performed on the correct type of equipment.
Access to each project is granted on an as-needed basis, and can be configured at the individual or group level so that each member of the team has only the access they need to be successful, and sensitive customer data is protected accordingly. Third party contractors can be granted focused access to the system, send notifications as needed, and exit the system seamlessly without any disruption to operations.
EXECUTION
Inspections can begin once project access has been granted, crews have been assigned, and third party contractors have been notified in the HUVR system. Technicians survey hazardous area equipment for potential sources of ignition, equipment condition, and common wear and tear.
Inspections are conducted in the field, typically capturing images and video footage, without the need for an internet connection. With offline capabilities and the ability to retroactively assign locations to data sets, contractors can conduct inspections in the field and upload the data once back online so that all captured media remains organized according to the assets inspected.
Using HUVR’s cloud-enabled all-in-one platform, technicians can store and stream mass quantities of media, eliminating the need for clunky USBs and hours of load time. The data can then be integrated with existing digital ecosystems as needed, and historical data can easily be accessed when it’s time to re-assess the condition of your assets. This gives technicians and subject matter experts a line of sight into the holistic integrity of your assets today, tomorrow, and five years down the road.
Reports are automatically generated in HUVR, giving technicians and asset owners a clear picture of the equipment integrity – no additional reporting tools needed. However, if you prefer to house your data in another system of record, HUVRdata’s Reliability Automation Platform integrates via standard API with virtually any business intelligence or inspection data management tool, including some of the most commonly used platforms in the industry like Meridium, SAP, Credo, and more.
REMEDIATION
HUVR’s reports and dashboards offer inspectors critical insights into the condition of their equipment. This enables them to swiftly and effectively address any identified issues – a crucial time-saving component when working with hazardous potential sources of ignition. Report formatting is configurable based on the asset owner’s requirements.
In cases where no issues are detected, asset condition information is uploaded to the cloud to inform future inspections, and the asset undergoes routine monitoring. If an issue has been identified, SMEs can be notified, they can easily review the findings, and are able to order replacements accordingly. The resolution is well documented throughout the process, providing a chain of history for future inspectors or asset owners reviewing large quantities of HAEQ inspections.
OUTCOME
Technicians and asset owners alike can now complete Hazardous Area Equipment inspections swiftly and easily in one place. Inspections completed in HUVR halve the time it takes to report on paper-based inspections, and make organization of mass quantity inspections a breeze. Historical data, previously hidden away or lost in paper and excel spreadsheets, can now be accessed anytime, providing asset owners with a more comprehensive view of their asset health and allows for higher quality monitoring and detection. Replacement decisions are made easier with comprehensive asset health history, and hazardous ignition risks are swiftly avoided thanks to HUVR’s all-in-one Reliability Automation Platform.
Want to learn more about our other cost-reducing workflows or speak with an expert to learn more? Check out our latest installment of the Workflows at Work series or schedule time with a HUVR expert here.