Blog · 8 MIN READ
Workflows at Work: Manual and Automated Operator Rounds
Posted on March 14
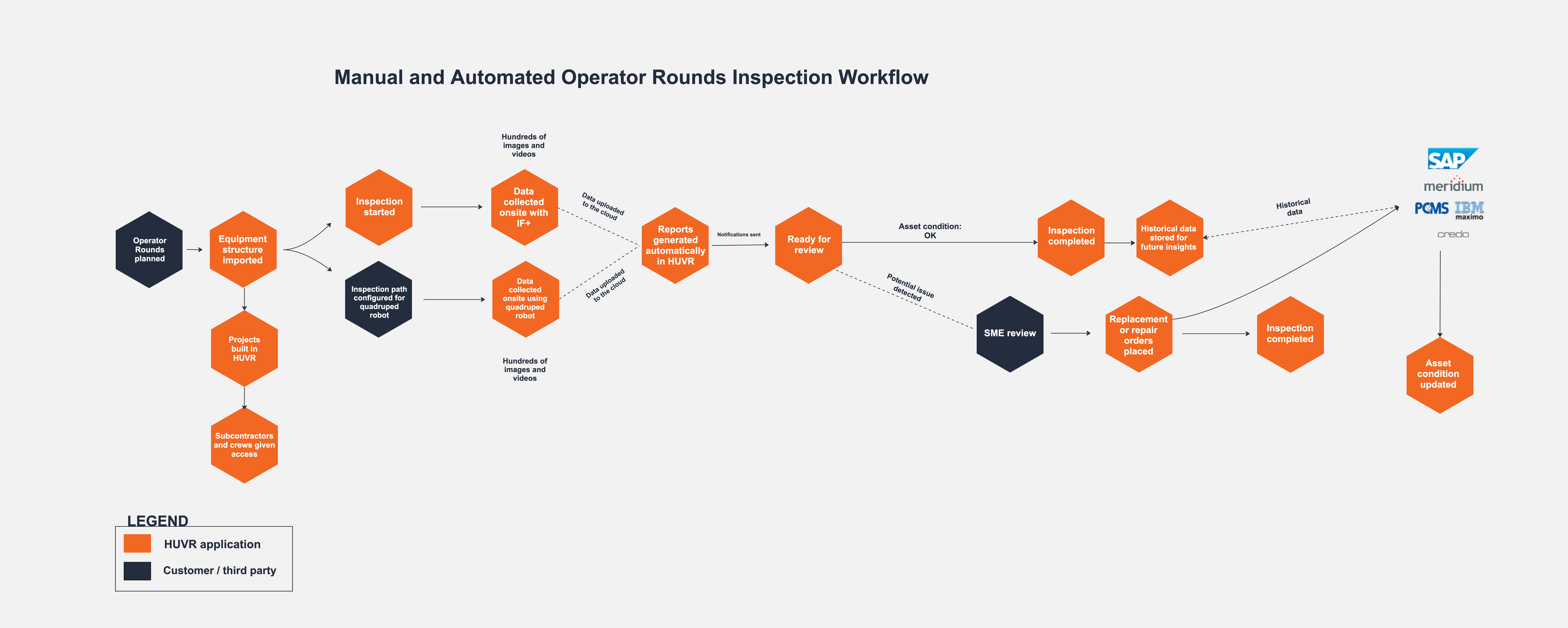
HUVR is proud to offer a wide range of inspection solutions that expedite and simplify your processes – each Workflows at Work piece in this series highlights one of the near-infinite workflows that HUVR optimizes. Curious about the simplicity and savings as you read? Reach out to an expert to ask about replicating this success with your business today.
Operator rounds: these swift but crucial visual inspections keep your plant running like a well-oiled machine; missed insights can lead to unplanned shutdowns, costing organizations like yours thousands of dollars in operational costs. During these critical exercises in maintenance excellence, expert technicians take to the field to routinely inspect assets and equipment critical to your plant’s operations up to three times a day, walking the site with a checklist in-hand. A problem with manual operator rounds? Paper-based checklists provide no visibility into urgent and historical insights and task progress while leaving too much up to interpretation when relying on descriptions of the condition of an asset. Additionally, paper-based processes like these require hours of work and high risk of re-entry errors when it’s time to transcribe the data from the field. Not to mention that tracking changes to routes becomes near impossible when the process is manual from end-to-end, and shift changes can be clunky and inefficient if not communicated effectively.
Technicians enabled with HUVR’s all-in-one Reliability Automation Platform leave all these issues in the past. Operator rounds traditionally done on paper can be digitized and seamlessly integrated with existing systems of record to improve efficiency, track changes to your assets overtime, track progress and round adjustments effectively, and manage workflows in one centralized hub. Additionally, as these routine checks join us in the digital age, robotics like quadrupeds can be deployed in the field as a proxy for on-the-ground technicians, creating efficient automated operator round workflows enabled by HUVR.
SET-UP
Digitizing your operator round inspection workflow is a process made simple with HUVR’s world class support team, who will work with you to build out your projects and digital checklists according to your needs. Asset owners can configure checklists, projects, and asset hierarchies with as much or as little granularity as needed for their respective plants and equipment. With the ever-changing landscape of regulations surrounding reliability and maintenance, your team can rest easy knowing every project is configurable in HUVR to comply with industry standards and provide your technicians with the guidelines they need for inspection success.
Checklists designed according to asset owners’ specifications are built with standardization in mind so that data comes back from the field in a clean, standardized format every time, no matter who is completing the inspection.
Security is paramount at HUVRdata. With HUVR’s tiered access model, each individual using the system only has access to the specific projects or datasets they need, eliminating confusion while keeping sensitive customer data privacy intact. Teams that need to manage large groups of inspections can be assigned to all projects and monitor progress via HUVR’s configurable dashboards that provide valuable insights into project statuses as they are completed.
EXECUTION
Once all the inspection projects are set up in the system and crews have been assigned, it’s time to complete your operator round inspections. Sometimes completed three times per day, these essential visual inspections can be completed manually by technicians in the field with their tablet in-hand, or automated with quadrupeds walking the site in the inspection team’s stead. Technicians or robot operators can be notified by the HUVR Reliability Automation platform when it’s time to inspect a particular asset or section of the site so inspections are completed in a timely manner.
Technicians using HUVR can easily access their checklists via the InspectFlow+ app with any standard iOS or android device in their pocket. With HUVR’s digital checklists and offline capabilities, inspectors can efficiently complete their inspections in a timely manner and immediately upload their findings once they have returned to a location with internet capabilities.
Technicians in the field will walk the site, inspecting analogue gauges, checking valve positions, and logging any odd smells, noises, or leaking products. Photos and videos can be recorded with ease in HUVR using any standard tablet or mobile device, minimizing confusion from reliance on individualized descriptions alone. With HUVR’s standardized, configurable checklists, technicians ensure data is logged in a standardized way, meaning operators receive good, clean, consistent data back from the field every time, regardless of subcontractor or in-house technician. Shift turnover is seamless for inspectors using HUVR as progress tracking and a digital chain of command are immediately available in the project view.
In automated operator rounds, paths can be built for routine inspections via quadruped robots.
Quadrupeds can walk the pre-programmed path, taking video as they move and inspecting gauges and valves as they proceed. With robotics on the ground as a proxy for technicians, on-the-ground teams can be more efficient, repurposing the time normally spent on these regular inspections to complete additional tasks and inspections in a timely manner.
Once data has been uploaded to the cloud, the HUVR Reliability Automation Platform makes it easy to notify SMEs and project leads that the inspection has been completed – technicians simply mark a project as complete, and the results can be automatically shared with the right team. With HUVR’s reporting and dashboard features, asset owners can also monitor progress across multiple projects at once, providing a holistic view of their teams’ progress and findings.
REMEDIATION
Once all the data has been uploaded and notifications have been sent, it’s time for review. Reports are generated from the field data collected near-instantaneously, and are sent to an SME for final confirmation. With outdated methods, data entry in the office would take a matter of days, transcribing information into spreadsheets that would be filed away to “sit on the shelf” indefinitely. With HUVR’s all-in-one Reliability Automation Platform, data is immediately made available, providing insights on the spot and allowing technicians to effectively redirect the time saved to more urgent tasks on the ground, creating direct cost savings for asset owners.
In cases where no issues are detected, asset condition information is stored to inform future inspections, and the asset continues to be routinely monitored. If an issue has been identified, SMEs can be notified, and can easily review the findings thanks to HUVR’s embedded and configurable report formats, ordering replacements or repair orders accordingly. The resolution is well documented throughout the process, and with HUVR’s API and native integrations, the historical data can be sent to any systems of record as needed for a comprehensive view across the board. Users now have a chain of history to inform future inspections and awareness of asset conditions.
OUTCOME
By utilizing HUVR’s manual and automated operator rounds, teams responsible for routine inspections can enhance efficiency and save time. With the click of a button, users can access comprehensive views of assets and project statuses, eliminating the cumbersome nature of paper checklists. This innovation makes shift turnover a seamless process and reduces the time spent on field and office activities, leading to increased productivity and efficiency gains.These efficiency gains translate to real dollars; meaning your teams are not only more efficient, but they’re also more profitable with HUVR.
Want to learn more about our other cost-reducing workflows or speak with an expert to learn more? Check out our latest installment of the Workflows at Work series or schedule time with a HUVR expert here.