Blog · 7 MIN READ
Workflows at Work: Remote Confined Space Inspections
Posted on May 07
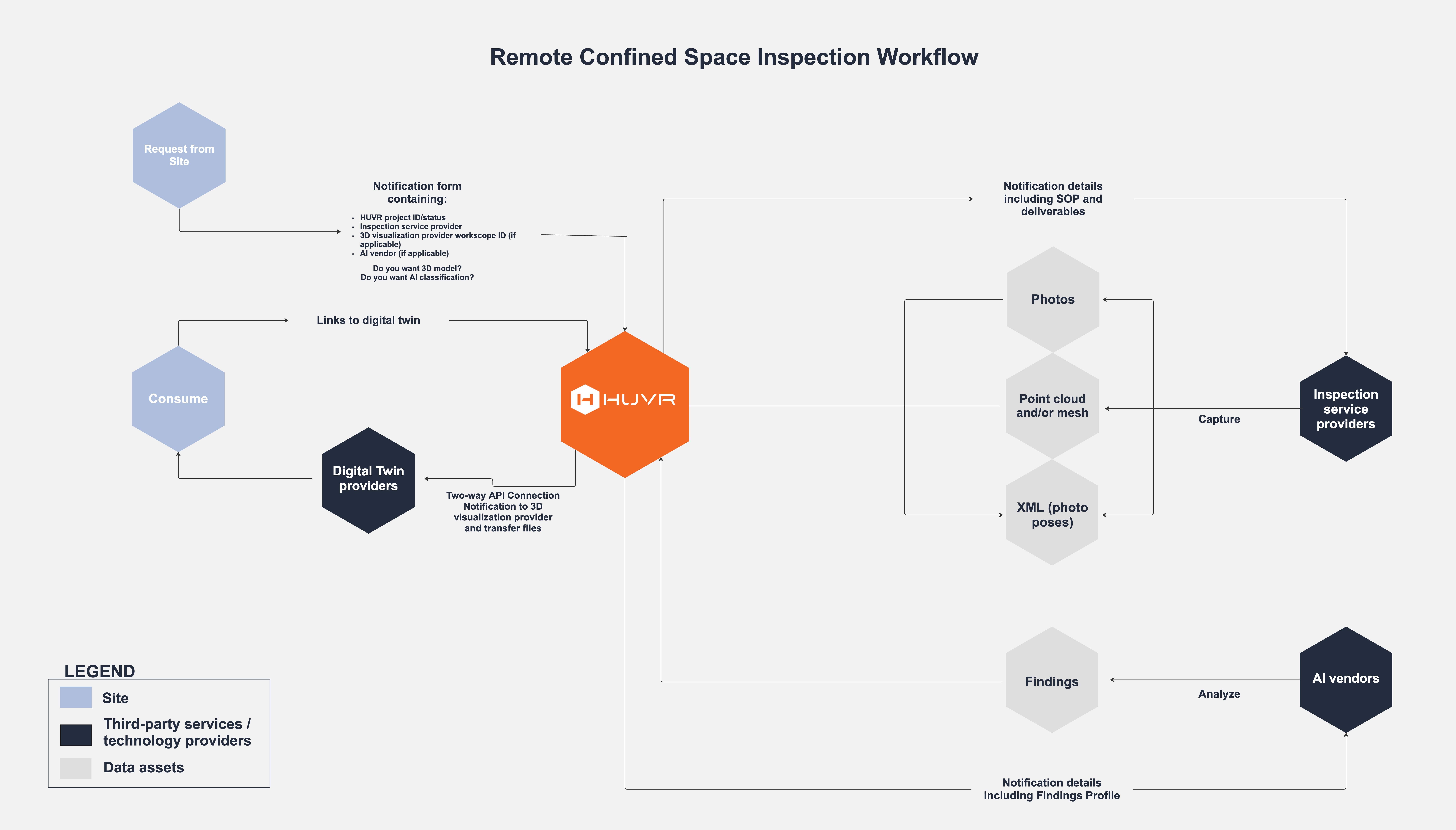
HUVR is proud to offer a wide range of inspection solutions that expedite and simplify your processes – each Workflows at Work piece in this series highlights one of the near-infinite workflows that HUVR optimizes. Curious about the simplicity and savings as you read? Reach out to an expert to ask about replicating this success with your business today.
Technicians working in confined spaces take on risk every time they enter a location not designed for human occupancy. When access is limited in these spaces, risks are increased for oxygen deficiency, hazardous chemicals, and highly flammable conditions. Whether it’s a storage tank, a cyclone, or pressure vessel, inspections in these spaces must be executed with safety top of mind.
In addition to the associated risk, confined space inspections can be more time-consuming and provide leaner data. HUVR’s remote inspection solution combines technology such as confined space inspection drones, indoor inspection drones, drones enabled with multi-sensor cameras, advanced crawler robots, and 3D models of the vessels in question. This wide array of data capture is richer, more standardized, and can be captured without a technician ever having to enter a confined space, meaning big savings when scaffolding costs can be reduced or eliminated in the process.
Confined space inspections completed remotely with HUVR save organizations like yours man-hours, costs, and risk. How, you might ask? It all starts with your standardized workflows built into HUVR.
SET-UP
Project set-up in HUVR’s Reliability Automation Platform is highly configurable to meet the needs of each organization’s equipment hierarchy. Projects are created automatically via systems integrations with your IDMS. Alternatively, HUVR offers a unique level of service in the industry: your dedicated support team will create and help manage projects on behalf of your sites, freeing up your time for other, more important matters.
Checklists and forms are built in the customer’s standardized format using set choices and language defined by the asset owner. This standardization allows technicians across multiple inspection service providers to perform inspections in HUVR consistently. The result is less guesswork when trying to interpret results across different vendors and clean, standardized data stored in the context of your equipment hierarchy alongside every other visual and NDE inspection performed on that equipment. Each checklist or form can be tailored to meet all the latest regulatory standards. Asset owners can also store general inspection practices and regulatory documents in each project so that technicians can swiftly reference them during inspections to ensure compliance with regulations and specific client needs.
The Principle of Least Privilege (PoLP) is applied to each project in HUVR. HUVR allows the flexible assignment of work to multiple crews and contractors. This means that contractors and inspectors only see the work that is assigned to them, but also allows collaboration between the two when needed.
EXECUTION
Once projects are set up and crews have been assigned, the inspection process can begin.
Traditionally, confined space inspections have been completed by technicians onsite, walking the plant with cameras and taking imagery within specifically defined areas. Costly scaffolding is often erected to support crews during their inspections, and tethering/harnessing is another added expense. The man hours, costs of inspection materials, and relatively limited data associated with boots-on-the-ground inspections can quickly add up.
Equipped with HUVR’s remote confined space workflows, you can gather rich data without ever having to send technicians into the equipment. Rather than sending a person into cramped and potentially hazardous equipment, drones can navigate these environments with precision. Drone operators guide the drones using radio controllers or tethers, enabling them to see what the tool sees in real-time.
These multisensor drones will fly into and around the vessel, capturing rich data consisting of video imagery, stills, and infrared scans. The data is then seamlessly uploaded into HUVR, the secure data hub for the entire inspection process from end to end. Clunky USBs or short-lived, hard-to-find share file sites are no longer needed as HUVR uploads the data from any internet-connected device to the cloud.
Once uploaded into HUVR, the imagery can be reviewed manually or the review can be augmented with internal or third party vision AI. HUVR offers a “human in the loop” approach to implementing vision AI. All Findings can be reviewed and edited efficiently directly within the platform. Any changes to findings data automatically go back to the AI solution provider to enable recursive learning and continuous improvement of their models.
Once the data review is complete, inspection reports are created automatically and the imagery is sent to 3D contextualization partners VEERUM or ZynQ360 to create a 3D model of the vessel where findings can readily be flagged, and automatically uploaded to the organization’s IDMS.
REMEDIATION
Findings can be overlayed onto the 3D model for deeper visual insights and a stronger understanding of the anomalies and overall asset health. Stored in HUVR, these findings are used to automatically generate reports embedded with imagery and data to make recommendations for remediation and create a chain of historical data to provide long term insights into asset health. The findings also seamlessly integrate with existing systems of record to ensure long term data continues to be saved and shared wherever it is needed.
Findings can then be used to make decisions about whether to repair parts of the vessel, or order replacement parts for pieces like vessel lining. Repair projects can be created in HUVR, and replacements can be tracked accordingly.
OUTCOME
Asset owners using HUVR for their remote confined space inspections can gather deeper, more holistic insights than man-on-the-ground inspections can. By sending autonomous or manually operated drones into the field instead, time on tools in the field is heavily reduced and technicians can complete inspections without ever having to enter a confined space. Risk is reduced by saving technicians the trip to these cramped and sometimes dangerous environments.
3D models overlayed with AI/ML-identified Findings linked to HUVR’s automatically generated reports provide rich, holistic views of vessels in question. The seamless integrations and options to review the findings expedite the review process so inspection teams have more time to spend on other inspections in the field or in the sky.
This newly freed up time, coupled with reductions in additional inspection costs like scaffolding or tethering create direct cost savings, making your teams not only safer and more efficient, but also more cost effective overall.
Want to learn more about our other cost-reducing workflows or speak with an expert to learn more? Check out our latest installment of the Workflows at Work series or schedule time with a HUVR expert here.