Blog · 8 MIN READ
Workflows at Work: Tank Seal Inspections
Posted on July 11
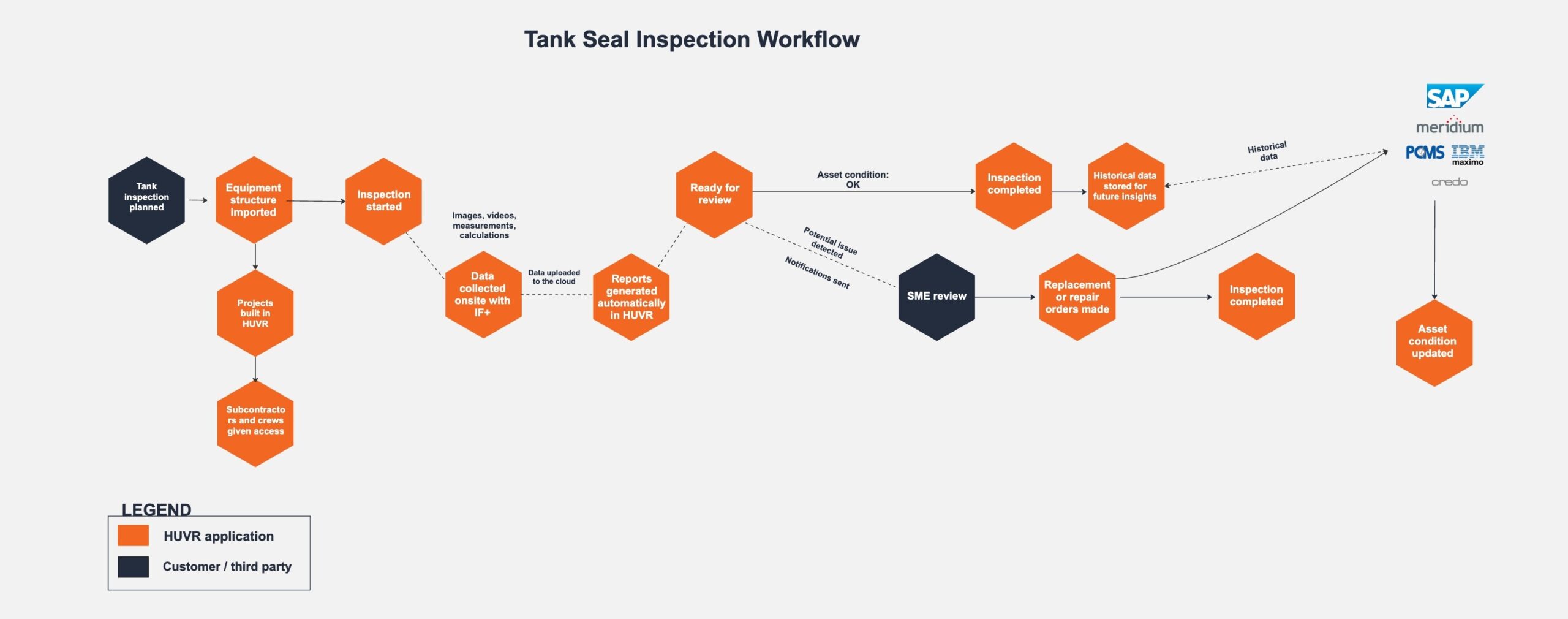
HUVR is proud to offer a wide range of inspection solutions that expedite and simplify your processes – each Workflows at Work piece in this series highlights one of the near-infinite workflows that HUVR optimizes. Curious about the simplicity and savings as you read? Reach out to an expert to ask about replicating this success with your business today.
As a wear-part that is essential to the success of tank operations, roof seals are a key component to inspect and maintain at regular intervals. Effective sealing prevents vapor leakage, reduces emissions, and minimizes product losses. As our technology evolves, so too do the regulations that dictate how, when, and what we inspect. With the advent of API Standard 653 and STI SP001, the difference between compliance and catastrophe with tank seals often comes down to a matter of mere inches. The comprehensive HUVR Tank Solution (HTS), designed with legacy Kinder Morgan tank expert Earl “the Tank Whisperer” Crochet, protects your organization from compliance issues and, with automatic calculations for tank seal inspections, can reduce error, save your teams time and money in manual calculations, and put the power of data back in the hands of your organization.
SET-UP
Project set-up is the first step to realizing tank seal inspection efficiency. HUVR’s Reliability Automation Platform offers flexible configurability, adapting project structures to the specific equipment hierarchy of any organization. Through seamless integration with an organization’s IDMS of choice, projects can be automatically created. HUVR’s world-class service team can also assist with creating and managing projects for your sites so you can focus on more critical priorities. However, HUVR users can always create and manage their own projects as needed, so that in the event an unexpected project arises or teams prefer to own the process, the power is in their hands.
Checklists and forms are built with required checks and measurements in line with the respective site’s regional standards and the customer’s preferred set choices and language. Standardizing the way the data is collected on site enables technicians from any inspection service provider to perform their tank seal inspections consistently in HUVR, delivering clean, report-ready results every time and removing guesswork from the interpretation of vendor inspection data. These checklists can then be assigned to the project in question, saved within the context of the organization’s equipment hierarchy alongside all other inspections performed on the tank or equipment, like UT, Radiography, or visual tank inspections. Regulation and general procedural documents can also be stored in the project so that technicians can quickly reference them during inspections to ensure compliance with regulations and client expectations.
Access is granted to projects in HUVR as needed so that crews, contractors, and inspectors alike can access the information they need – and only the information they need.
EXECUTION
Once a crew member has been assigned to their project, they will receive notifications when it’s time to complete the inspection. The system is built to automatically notify crew members when it’s time to inspect the asset in accordance with standard requirements. These standards vary according to location, and federal regulations may require one standard while state and local municipalities may demand another with higher frequency. Technicians using HUVR no longer need to be concerned with planning this on their end – we work directly with the site to configure intervals that keep your organization compliant no matter where you are.
Rather than handling clunky paper checklists and manually calculating measurements with a calculator, API653-certified technicians can use HUVR’s field app, InspectFlow+, on any Android or iOS-enabled device to collect the tank seal data. Technicians using InspectFlow+ will take pictures of the asset’s condition and input measurements for the maximum width, average width, and length of any gaps between the seal and the tank via their phone or tablet.
Based on the diameter of the tank in question, the checklist will then automatically calculate the area of each gap and the surface area of all gaps between the seal and the tank. Images provide richer, more clear data on the asset’s condition so owner/operators no longer have to rely on subjective descriptions. Additionally, by taking manual calculations out of the equation, the chance for human error and time in the field spent calculating is significantly reduced. The process is also much simpler and faster when using a mobile device in lieu of unwieldy paper and pencil checklists alongside physical rulers or calipers.
Once measurements and calculations are complete, depending on the size of the tank and the respective standards for permitted gap size, the technician can then mark in HUVR whether the tank seals have passed or failed inspection. Requirements for what information is collected and what kind of gap sizes are allowed will vary depending on the region’s standard. The EPA requires measurements be reported in square inches, and gap size permission is determined by specific standards like API653 or STI SP001.
Once the technician returns to a location with connectivity, the data is uploaded and the project can be marked complete. The findings are then reviewed by SMEs and reports with embedded imagery can be created automatically, detailing the findings. Owner/operators can monitor progress in real-time with HUVR configurable dashboards, keeping track of asset condition and inspection progress every step of the way.
REMEDIATION
Once a tank seal has been determined to pass or fail, steps for remediation can be taken. A tank seal has failed inspection if the seal gaps exceed a maximum gap width or surface area limit. The tank has passed if it is within limits. Depending on how close to the limit the seal is, additional inspections may be planned in advance of the next regularly scheduled inspections to closely monitor the condition of the asset and prevent costly leakage.
If a tank seal has failed inspection, remediation takes effect. For out-of-service tanks being prepared for a return to service, seal replacements are a common choice. Repairs are more common for in-service tank remediation. Repair orders can be created in HUVR to notify respective teams so that all of your reliability and maintenance inspection processes can be completed in one centralized location.
If a tank seal passes inspection, no further action is required. The data is stored indefinitely in HUVR and integrates directly with existing systems of record like SAP or Meridium, creating a historical chain of command to inform long-term insights about asset health. With a set schedule for inspections, notifications will be sent automatically when inspection time rolls around again in the future so your team can stay focused on the work orders that matter most when they need it most.
OUTCOME
Planning, execution, and reporting are simplified in one pane of glass with HUVR.
Teams using HUVR’s interoperable all-in-one system for their tank seal inspections gather better data, complete inspections more efficiently, and are able to monitor asset conditions longterm with ease. Thanks to HUVR…
- Data gathered using configurable checklists comes back from the field in a standardized, clean way so findings are consistent
- Teams no longer have to rely on subjective reporting methods to understand the condition of their tanks and tank seals, taking imagery as they go
- Automatic calculations save teams time and money, significantly reducing the chance for human reporting errors
- Reporting is simpler and progress can be monitored in real-time
- A historical chain of command is now available to inform better long-term insights into asset health
Improve your team’s operational efficiencies in the field with HUVR – reach out to an expert to learn more about how HUVR can revolutionize your tank inspections and improve ROI today.
Want to learn more about our other cost-reducing workflows or speak with an expert to learn more? Check out our latest installment of the Workflows at Work series or schedule time with a HUVR expert here.